Top Uses of a Dial Indicator in Industrial Applications
- Abdul-Alim Mihran
- Dec 2, 2024
- 5 min read
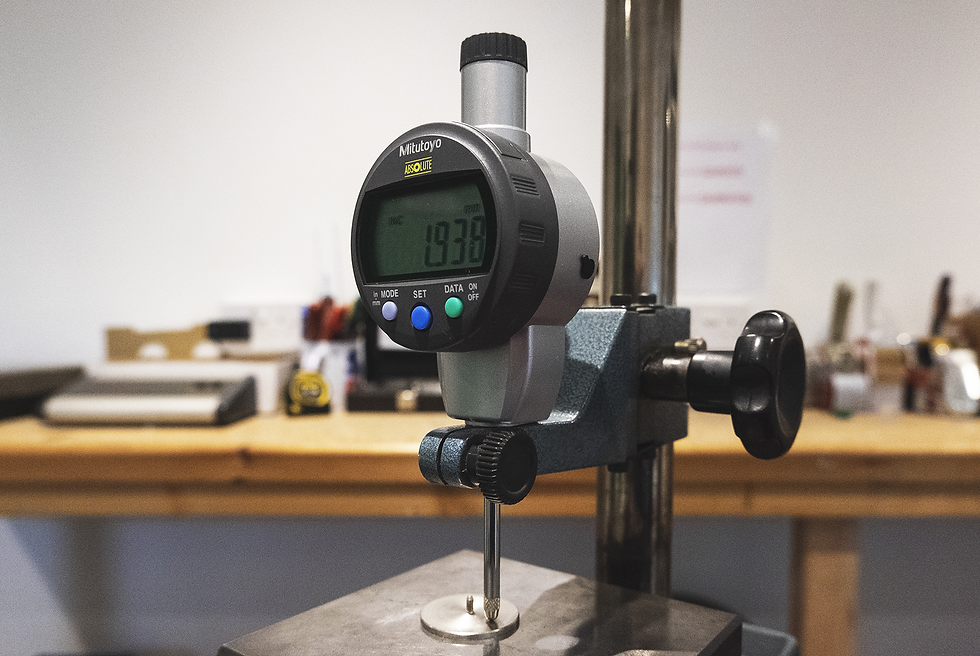
Dial indicators are essential tools in industrial settings, where precision and accuracy are non-negotiable. From aligning machinery to ensuring flawless quality control, these devices play a pivotal role in optimizing processes and preventing costly errors. But what makes them so indispensable? Let’s dive into the mechanics, uses, and advantages of dial indicators in industrial applications.
What is a Dial Indicator?
A dial indicator is a precision measurement tool that provides accurate readings of small distances or deviations. Its key components include a dial face, a needle, and a plunger or probe that moves to indicate measurements. These instruments come in analog and digital forms, catering to various industrial needs.
How Does a Dial Indicator Work?
The basic working principle of a dial indicator involves translating linear motion into readable measurements. When the probe is displaced, the needle on the dial face moves to reflect the exact deviation.
Analog vs. Digital: While analog indicators use a needle for measurements, digital ones display readings electronically, often offering additional features like data logging.
Applications of Dial Indicators in Industries
Alignment and Calibration
Misalignment in machinery can lead to inefficiency and damage. Dial indicators ensure precision in aligning machine components, reducing downtime and improving productivity.
Common tasks include aligning motors, shafts, and gears.
Measuring Surface Flatness
Flatness is crucial in manufacturing processes. Dial indicators are commonly used to check the flatness of surfaces, ensuring products meet strict specifications and perform as intended.
Measuring Shaft Runout
Shaft runout refers to the deviation of a shaft from its true rotational axis. A dial indicator helps detect these deviations, preventing mechanical failure in critical systems.
Setting Up Precision Tools
Dial indicators assist in setting up lathes, milling machines, and grinders with precision, ensuring tools perform consistently. This is vital in tasks requiring repeatable accuracy.
Inspecting Roundness
Industries like automotive and aerospace rely on dial indicators to check the roundness of components such as bearings, gears, and cylinders. Any deviation can compromise safety and efficiency.
Advantages of Using Dial Indicators
High Accuracy: Provides precise measurements critical for industrial tasks.
Versatility: Suitable for various applications, from calibration to quality control.
Durability: Designed to withstand demanding industrial environments.
Limitations of Dial Indicators
Despite their utility, dial indicators have some limitations:
Sensitivity to Vibrations: External vibrations can affect accuracy.
Learning Curve: Proper usage requires skill and training.
Analog vs. Digital: While digital models are more advanced, they may require batteries or specific conditions to function optimally.
How to Choose the Right Dial Indicator
Selecting the right dial indicator depends on your specific needs:
Range: The maximum measurement it can handle.
Resolution: The smallest detectable change.
Sensitivity: How responsive the indicator is to minute changes.
Maintenance Tips for Dial Indicators
Keep it Clean: Dust and debris can affect performance.
Calibrate Regularly: Ensure the readings remain accurate over time.
Proper Storage: Store in a protective case to prevent damage.
Ensuring Machine Alignment
In industries reliant on large machines, proper alignment is crucial. Dial indicators are used to align machine components such as shafts, spindles, and pulleys.
Horizontal and Vertical Alignment: Measures discrepancies in shaft alignments.
Rotational Alignment: Ensures precision in rotating machinery, reducing wear and tear.
Efficiency Boost: Correct alignment improves machine longevity and performance.
Measuring Runout
Runout refers to the deviation of a surface as it rotates. Dial indicators are widely used to measure runout in various components, including shafts and wheels.
Lateral Runout: Measures side-to-side deviations.
Radial Runout: Determines the concentricity of rotating components.
Critical for Safety: Ensures parts like brakes and rotors function properly.
Checking Flatness and Parallelism
Flatness and parallelism are key in machining and assembly processes. Dial indicators assess the evenness of surfaces, ensuring precision assembly.
Flatness Tests: Verifies that surfaces are level.
Parallelism: Ensures multiple surfaces are parallel, especially in molds and dies.
Improved Fit and Functionality: Guarantees that parts assemble seamlessly.
Measuring Thickness and Depth
Dial indicators excel in applications where precise thickness or depth measurements are required.
Thickness Gauging: Measures material thickness in production lines.
Depth Measurement: Assesses the depth of drilled holes, slots, or recesses.
Enhanced Consistency: Ensures uniformity in production.
Detecting Surface Irregularities
Surface imperfections can compromise the quality of finished products. Dial indicators help identify such irregularities with pinpoint accuracy.
Surface Roughness: Measures small variations that may affect functionality.
Wave and Bow Checks: Identifies undulations in large surfaces.
Quality Assurance: Improves the visual and functional appeal of components.
Verifying Tolerances in Manufacturing
Tolerances are the allowable limits of variation in a part's dimensions. Dial indicators ensure that manufactured parts fall within specified tolerances.
Dimensional Accuracy: Confirms that parts meet design specifications.
Tool Calibration: Ensures machine tools are functioning within tolerances.
Minimized Waste: Reduces material wastage by detecting errors early.
Inspecting Bearings and Shafts
Bearing and shaft integrity are vital for machinery performance. Dial indicators detect wear, misalignment, and other issues.
Bearing Checks: Identifies excessive play or looseness.
Shaft Integrity: Ensures straightness and proper fitting.
Prevents Downtime: Detects issues before they escalate into costly repairs.
Monitoring Gear Accuracy
Dial indicators are indispensable for inspecting gears, ensuring smooth operations in transmission systems.
Tooth Alignment: Verifies uniform spacing and alignment of gear teeth.
Backlash Measurement: Determines the gap between mating gear teeth.
Enhanced Performance: Ensures quiet and efficient gear operation.
Testing Concentricity
Concentricity measures how well a part's features align around a central axis. Dial indicators excel in assessing concentricity in cylindrical components.
Roundness Testing: Evaluates uniformity in round components.
Critical for Rotational Parts: Ensures stability in spinning components like turbines.
Precision Fit: Guarantees better functionality in assembled parts.
Balancing Rotating Machinery
Unbalanced rotating machinery can cause vibrations, leading to premature wear or failure. Dial indicators help achieve perfect balance.
Dynamic Balancing: Ensures smooth operation of rotating parts like fans and pumps.
Static Balancing: Detects imbalances in stationary components.
Reduced Vibrations: Enhances machine reliability and safety.
FAQs
What industries commonly use dial indicators?
Dial indicators are widely used in machining, automotive, aerospace, and manufacturing industries.
How do I choose the right dial indicator for industrial use?
Consider the measurement range, accuracy, type (plunger or lever), and build quality based on your application.
Yes, lever-type dial indicators are particularly suited for measuring curved or angled surfaces.
How often should a dial indicator be calibrated?
Regular calibration is recommended, ideally before critical projects or after extended use.
What is the typical accuracy of a dial indicator?
Most dial indicators offer accuracy up to 0.001 inches or 0.01 millimeters.
Is a digital dial indicator better for industrial applications?
Digital dial indicators provide easier readings and additional features, but analog versions remain reliable for many tasks.
Conclusion:
Dial indicators are a vital tool in industrial applications, ensuring accuracy, efficiency, and safety across various tasks. From aligning machinery to verifying tolerances, they are indispensable for professionals who demand precision. By understanding their uses and benefits, businesses can harness the full potential of these tools to achieve exceptional results
Comments